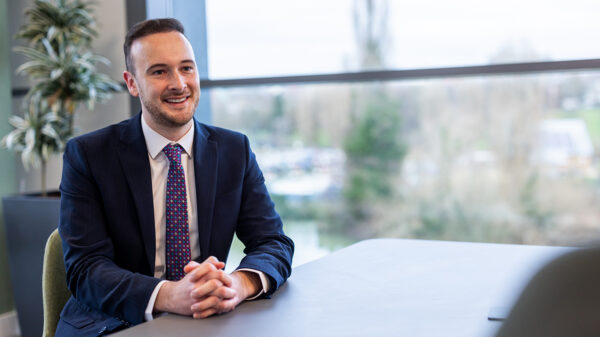
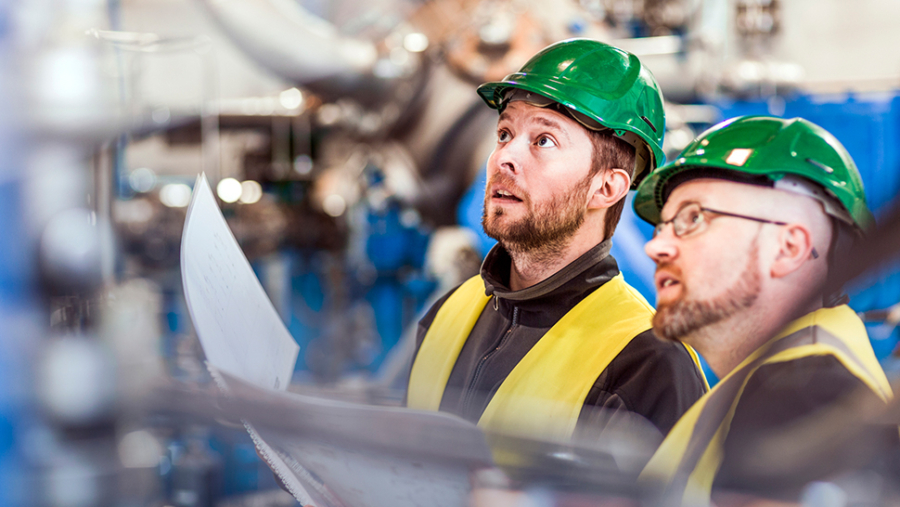
As part of our In-House with You monthly Q&A series, insurance specialist Jonathan Edwards spoke about the key aspects of a health and safety investigation, handling investigators, preventing recurrence and more. The slides can be accessed here.
Jonathan answers some of your key questions below:
Why do companies not invest more in planning?
Risk management is often seen as a cost, not an investment, and many companies say they have more pressing priorities. It surprises me how little some companies actually invest in doing what’s necessary to identify and put in place measures to control key business risk. Implementing appropriate measures will put you in the best position to deal with critical incidents when they arise, and they invariably will. Planning should never be regarded as a waste of resource or operational time.
How many companies that you’ve worked with test their plan? Do you feel the test should be carried out as a blind examination, where no-one has been briefed – “an incident has happened, let’s see where it rolls to/see who gets information through”?
Testing your incident management plan to see if it’s “fit for purpose” is vital. Companies who properly plan and have thought through the variety of scenarios that might arise from an incident are much more likely to maintain control and achieve stronger outcomes, reputationally and financially. Those organisations who adopt the ‘we’ll manage, it won’t happen to us’ attitude, will very likely be caught off-guard and with no response team in place, quickly lose control of the narrative and be considerable worse off for the experience. Identify the strongest team to respond to a particular incident, depending on the nature of the potential incident it might not always involve the same personalities, bring them together, run scenarios and learn: what went well, what didn’t. Adjust the plan to take account of the lessons learned and keep under review. Involve external advisers when testing, as you will need them when the incident occurs for real. You will want to be clear on how the business may be able to invoke “legal privilege” to protect its internal investigation from external scrutiny, and not do anything which may then waive that privilege.
If during an investigation, it becomes apparent that improvements should be made, should we make them or should we await the outcome of any external investigation or claim?
If during an investigation, you identify an issue, whether that be with e.g. equipment or a work process, implementing an improvement doesn’t necessarily mean that you will be found legally liable for the incident that occurred. If having identified an issue, you do not address it and another similar incident were to occur the financial and reputational cost is likely to be significantly greater. Your failure to act will be seen as an aggravating feature in any subsequent investigation and prosecution, let alone the harmful messages it sends out to your customers and potential customers about your business.
Is it easier to leave the “actions required to prevent a recurrence” box out of an accident reporting form?
The problem with this box is that the person completing the accident report, more often than not, feels compelled to fill it in, whether they are qualified to do so or not. Knee-jerk reactions are all too common place. Once the comment has been made it is often extremely difficult to displace and leaves you very exposed to prosecution and/or civil claims. Nothing should be written down until you are sure that what is being committed to writing is accurate. Keep the report factual – this is not a document that should record opinion. Once the investigation is complete, the individuals engaged in carrying it out should meet to discuss their findings and then agree what should be entered on the accident report. This will avoid misplaced comment and unsubstantiated speculation.
There’s a requirement in the H&S Act to have a H&S policy. If you’ve got a very slim H&S policy that doesn’t say very much, is that sufficient to meet the requirement if you’re investigated or would that be considered a minus?
Every business must have a policy for managing health and safety. This policy must be a written document where you engage five or more employees. Where you engage less than 5 employees you do not need to do so but the HSE recommends you do, and I agree.
The policy should set out your general approach to health and safety, and explain how you, as an employer, will manage health and safety in your business. It should clearly say who does what, when and how.
Quality over quantity is the key, make sure your policy contains all the important and relevant information, and that people in your employ understand what is in the policy and how and by whom it will be implemented. Keep the policy under regular review and update as required. Make sure any changes are effectively communicated and understood. Communication, as with so many things, is key.
When should I carry out a specific keep risk assessment?
Organisations need to think carefully about work activities which aren’t adequately covered by a generic risk assessment. For a risk assessment to be effective in reducing the risks, it must identify the hazards that are foreseeable and significant. It must then evaluate the risks, which will assist in determining appropriate control measures. Risk assessments should be carried out against specific work activities that carry risks which may not have been identified in a generic risk assessment. Carefully review existing risk assessments to satisfy yourself that the risks associated with the task have all been addressed and that the control measures remain appropriate. If not, prepare a task specific risk assessment. Communicate the findings of the risk assessment to all employees who will be engaged on the task. Make sure they understand the risks and the control measures. Invite feedback. Revise the assessment as required and make sure any changes are communicated. Ensure the control measures are all in place before the work begins and are properly maintained throughout. Risks change, so review regularly and ensure the control measures remain relevant.
What sort of records can a H&S team provide that might be strongest? Examples of inspections? Reviews of risk assessments? Action tracking?
Documents relating to inductions, training, instructions, risks assessments, systems of work and records of regular review are typical examples of the evidence you will need to produce during an investigation. Bear in mind that the HSE’s success rate when prosecuting is in excess of 90% which is really significant, largely because of s.40 HSWA which reverses the burden of proof so that the duty holder must prove that it was not practicable, or not reasonably practicable to do more than was done, or that there was no better practicable means than that used to satisfy the duty or requirement. So, there are lots of things to think about before embarking on a defence, including the potentially significant discount available for an early plea.
Many companies are tightening the purse strings – especially in construction – will that increase the likelihood of bad practice and incidents?
Yes, without any doubt at all. There is always the danger that companies, particularly those with limited resources and funds, will run the risk, take shortcuts, and pay the price. This is likely to rebound badly when an incident occurs (as it often does in such circumstances), being viewed as profit over safety.