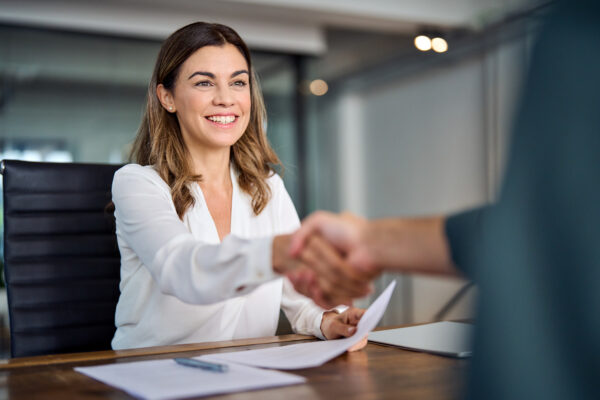
Meat processing plants as centres of infection – what’s being done and what needs to be done?
10 July 2020
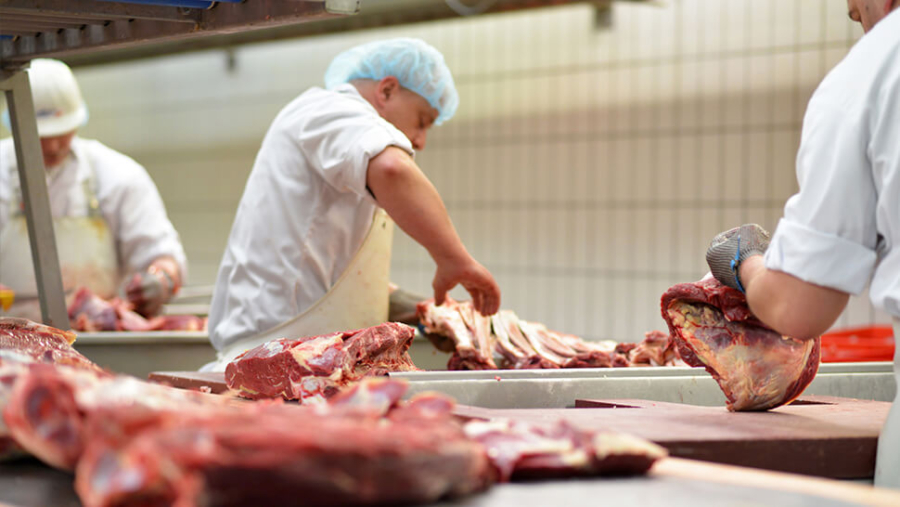
Many of us will have seen reports of the hundreds of workers who have tested positive for coronavirus at meat processing plants and abattoirs.
Clusters of infections have arisen all round the world, including Germany, France, Spain and the US and closer to home, in Anglesey, Wrexham, Merthyr Tydfil and Yorkshire.
Why are meat processing plants and abattoirs seeing such high levels of infection?
Many scientists and specialists in the field have stated that factories and plants offer perfect environments for the virus to spread and linger. They are indoor areas that are cold and damp and lack natural light. Refrigerated workplaces are also noisy, requiring people to talk loudly or shout – instances of people removing masks to aid communication, increasing the spread of droplets, are thought to be common. Further, fast moving production lines pose particular problems for social distancing and keeping two metres apart. Workers have anonymously reported in the press that social distancing in these environments is impossible.
The situation is worsened by the fact that many plants and abattoirs have Eastern European staff who have had poor training and do not have good language skills.
Large numbers are also not entitled to full sick pay, so could lose pay if they self-isolate after getting sick. Indeed, this latter concern has been reported by workers at Rowan Foods, Wrexham.
The duties and responsibilities of businesses
Businesses have a number of duties and responsibilities to take all reasonably practicable steps to ensure the health, safety and welfare of workers. This is outlined under the Health and Safety at Work Act 1974 and under other regulations such as the Management of Health and Safety at Work Regulations 1999 and Personal Protective Equipment at Work Regulations 1992. In Wales, businesses have a specific statutory duty under the Health Protection (Coronavirus Restrictions) (Wales) Regulations 2020 to take all reasonable measures to ensure that a distance of two metres is maintained between persons on premises.
Guidance for food manufacturing businesses working during the Covid-19 pandemic
Guidance has been produced by the Food Standards Agency (FSA) to help businesses and staff work safely in the food manufacturing sector during the Covid-19 pandemic. It focuses on the hygiene processes and requirements you must follow to continue to safely operate your business. The guidance should be read in conjunction with wider government advice on Covid-19 so you can understand the practical framework needed to identify and protect against risks.
Central and fundamental to the approach to protect employees and promote a healthy work environment is the need to conduct a bespoke Covid-19 risk assessment using the government social distancing guidance to inform decisions and control measures.
The steps needed to guard against Covid-19 risks will need to be dovetailed with existing food safety management systems.
As far as risk assessments are concerned, the Health and Safety Executive (HSE) states you must:
- identify what work activity or situations might cause transmission of the virus;
- think about who could be at risk;
- decide how likely it is that someone could be exposed;
- act to remove the activity or situation, or if this isn’t possible, control the risk.
The British Meat Processors Association (BMPA) has also issued guidance, including cleaning factories more often than usual, isolating staff who develop symptoms and staggering start and break times. It also suggests providing additional personal protective equipment (PPE) such as visors, if available. Staff in meat processing facilities usually wear PPE, as set out in their relevant Food Safety Management Systems (FSMS) and in line with Health and Safety at Work policies. However, it does not necessarily include masks.
Regulatory and enforcement action for breaches of health and safety regulations
A breach of the health and safety legislation can be subject to regulatory and enforcement action which, on conviction, can lead to a fine. Civil claims can also be pursued by affected workers for damages for personal injury.
Interesting causation arguments are likely to arise when looking at infections in these factory environments.
For regulatory prosecutions there will need to be a sound body of expert evidence that infections, on balance, were caused by exposure to the virus via particular workplace failings, rather than wider, community-related transmission. Where only a few cases arise in a workplace, it may actually be quite difficult to prove this. However, with clusters of confirmed cases, such as those we have seen in meat processing plants and similar facilities, it will be possible to presume that exposure probably occurred in that workplace. This aspect will be an interesting battleground in the regulatory arena and time will show the nature of the arguments to be raised in this regard.
The importance of conducting bespoke, collaborative risk assessments
There can be no doubt that a return to the workplace brings an increased risk of transmission. This is even more the case in the meat processing sector and so the duty and measures taken to protect staff will be placed under particular focus.
Failure to conduct a bespoke risk assessment will expose staff to much higher risk and invite the strongest regulatory action. To prevent action being taken by the regulatory bodies it will be important to engage staff and document decision making and risk assessments as far as practically possible.